Camera Engineering
Real-Time Vision System for Industrial Drone Camera
Client Background:
Regami collaborated with a leading industrial drone manufacturer specializing in aerial inspections. These drones, equipped with high-resolution cameras and sensors, are used to capture detailed imagery for industrial applications. However, the client’s existing image processing system faced significant delays in real-time defect detection, slowing down inspection workflows.
To address these issues, they partnered with Regami to optimize processing speed, enhance image quality, and improve system performance in demanding environments.
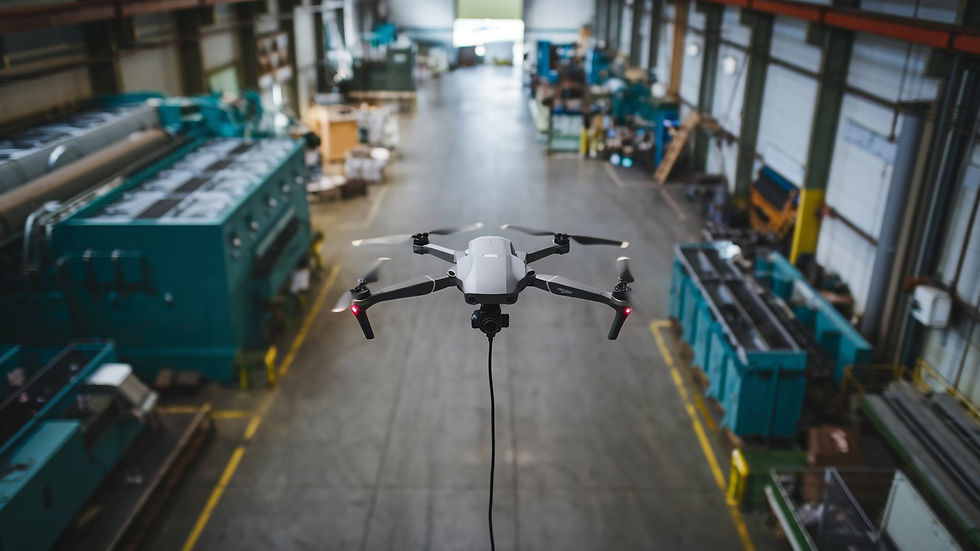
Challenges:
The client faced significant challenges with their existing system, including high latency in processing high-resolution images, which delayed real-time defect detection. Image quality issues, such as poor performance in low-light and HDR conditions, and lens distortion, further hindered accurate diagnostics. Additionally, managing large data volumes during high-speed flights strained the system, while the non-scalable architecture limited future upgrades. The user interface also lacked real-time feedback, making timely decision-making difficult during inspections.
The client sought a solution from Regami to address these issues, enhancing processing speed, image quality, scalability, and real-time feedback for improved inspection accuracy and efficiency.
Our Solutions:
Regami implemented a series of tailored enhancements to transform the client’s drone vision system:
Simplified Real-Time Visual Control: We revamped the user interface for intuitive interaction, enabling operators to zoom into critical areas, identify defects quickly, and streamline decision-making.
Advanced Image Data Optimization: Efficient compression algorithms were deployed to minimize bandwidth requirements while maintaining image quality, ensuring smooth real-time image rendering during operations.
Dynamic Image Adaptation: Integrated adaptive resolution and compression mechanisms to optimize performance under varying bandwidth and resource conditions, ensuring consistent functionality across diverse environments.
Enhanced Sensor Integration: High-resolution sensors were fully optimized to capture detailed imagery without overwhelming the hardware, improving the accuracy and reliability of data collection.
High-Speed Data Processing Pipeline: A streamlined data transmission system was developed to reduce latency, enabling real-time actionable insights and rapid decision-making during inspections.
HDR and Low Light Enhancements: Image signal processing was fine-tuned for challenging lighting conditions, delivering clear and detailed images in low-light and HDR environments.
Outcomes:
The implemented solutions delivered significant improvements in the drone vision system's efficiency, accuracy, and scalability:
Real-Time Optimization: Faster processing enabled real-time defect detection, reducing downtime and accelerating inspection workflows.
Enhanced Processing Speed: Optimized pipelines reduced image processing time by half, ensuring quicker response times during critical inspections.
Superior Image Resolution: Improved clarity in low-light and HDR conditions enabled more reliable defect detection, even in challenging environments.
Refined Accuracy Metrics: Enhanced image quality and processing speed increased the accuracy of defect detection, ensuring more thorough and dependable inspections.
Optimized Drone Performance: Efficient data handling improved the drones' overall performance, allowing stable and effective operations even at high speeds or in complex flight conditions.
Scalable System Architecture: The modular design supports seamless integration of future sensor technologies, ensuring long-term adaptability and cost-effective system upgrades.